Retrofitting 4.0: Casos Reales de Maquinaria Antigua Adaptada a la Industria 4.0
Si trabajas en una planta industrial, seguro que convives con máquinas que llevan décadas funcionando. Son robustas, fiables y han demostrado su valor, pero ahora enfrentan un desafío: la digitalización. ¿Cómo integrarlas en la Industria 4.0 sin que suponga un gasto desorbitado?
OT e IT: un desencuentro que ya no tiene sentido
Hasta hace poco, el mundo de la automatización industrial (OT) y el de la tecnología de la información (IT) vivían de espaldas el uno al otro. Esto ha creado barreras que complican la digitalización:
- Protocolos de comunicación propietarios: muchas máquinas utilizan protocolos antiguos y cerrados que no “hablan” con los actuales.
- Falta de conectividad moderna: muchas ni si quiera disponen de módulo de entrada ethernet o protocolos de comunicación estándares como OPC-UA.
- Falta de estandarización: aunque las nuevas máquinas suelen estar diseñadas para integrarse en entornos digitales, las antiguas no cuentan con los sensores, conectores o software necesario para intercambiar datos en tiempo real.
El reto principal es integrar equipos diseñados para operar de forma independiente en un entorno donde los datos son el corazón de la operación.
Según Oracle, los problemas de interoperabilidad y la complejidad de integrar sistemas heredados son algunos de los mayores obstáculos para la adopción de la Industria 4.0, limitando la conectividad y el aprovechamiento de nuevas tecnologías.
Retrofitting industrial: la solución inteligente
El retrofitting consiste en darle una segunda vida a tu maquinaria actual, sin necesidad de invertir en nuevos equipos. ¿Cómo se logra? Incorporando tecnología que le permita conectarse e integrarse con el resto de tu sistema.
Casos de retrofitting: de lo simple a lo complejo:
Situaciones más sencillas:
- Sensores: instalar sensores que monitoricen variables clave como temperatura, vibraciones o velocidad. Estos sensores generan datos que se pueden integrar en sistemas de análisis.
- Gateways de comunicación: incorporar dispositivos que traduzcan protocolos antiguos a estándares modernos, como OPC-UA o MQTT. Esto permite que las máquinas envíen datos a sistemas IT (ej. MES, ERP, GMAO).
Nivel intermedio:
- Actualización de PLCs: reemplazar o actualizar el PLC existente para que soporte conectividad Ethernet y protocolos modernos.
- Integración de Edge Computing: incorporar dispositivos Edge que procesen los datos localmente antes de enviarlos a la nube, mejorando la latencia y reduciendo la dependencia de la conectividad.
Situaciones complejas:
- Automatización completa: renovar los sistemas de control de la máquina, incluyendo nuevos servomotores, drivers y software.
- Empresas especializadas: en casos donde el retrofitting requiere un nivel de personalización elevado, es necesario trabajar con empresas de automatización industrial que desarrollen soluciones a medida.
Caso de éxito: Mein - Funcasa
Funcasa necesitaba sustituir varios elementos de control obsoletos en su planta industrial. El desafío consistía en modernizar sus sistemas sin interrumpir la operación ni realizar grandes inversiones en maquinaria nueva.
Instalaciones de Fundición en Cáscara, FUNCASA - MEIN.
¿Cómo lo abordamos?
- Módulos de comunicación Ethernet: integramos módulos de comunicación que permitieron conectar las máquinas antiguas a redes basadas en Profinet, facilitando la integración con sistemas IT modernos.
- Actualización de paneles de operador: reemplazamos los paneles HMI por modelos táctiles de última generación, mejorando la interfaz de usuario y la gestión de datos en tiempo real.
- Optimización de programas PLC: realizamos ajustes en los programas de control para optimizar la comunicación y el rendimiento de las máquinas.
Resultados:
- Mayor visibilidad de los datos de operación, lo que permitió un mejor control de la producción.
- Reducción de tiempos de inactividad no planificados.
- Mejora de la eficiencia operativa sin necesidad de invertir en maquinaria nueva.
Caso de éxito: empresa de estampación y prensado
En esta empresa, la información de las máquinas se capturaba de forma manual, lo que generaba imprecisiones y dificultaba la obtención de datos en tiempo real. Su objetivo era empezar a analizar los datos de dos perfiladoras antiguas, fabricadas por distintos proveedores, pero se encontraron con una limitación técnica importante: los PLCs instalados en estas máquinas estaban obsoletos, lo que imposibilitaba la captura automatizada de datos esenciales para su operativa.
¿Cómo lo abordamos?
- Reacondicionamiento de PLCs: los acompañamos en la elección de nuevos PLCs compatibles con sus máquinas, asegurando la captación de datos críticos y la integración con sistemas modernos.
- Asesoramiento técnico: guiamos al cliente durante todo el proceso, desde la recomendación de proveedores hasta la implementación de los nuevos sistemas, adaptándonos a su ritmo de adopción tecnológica.
Resultados:
- Captura de datos precisos para la toma de decisiones basada en información confiable.
- Visión en tiempo real del rendimiento de la planta, mejorando la capacidad de respuesta ante incidencias.
- Optimización de la eficiencia operativa, reduciendo errores y mejorando la calidad de los procesos.
El enfoque llave en mano de Savvy
En Savvy Data Systems ofrecemos proyectos llave en mano que simplifican la integración de maquinaria antigua en la Industria 4.0. Nuestro enfoque incluye:
- Diagnóstico inicial: analizamos el estado actual de la maquinaria y los sistemas de la planta para identificar oportunidades concretas de digitalización.
- Diseño de soluciones personalizadas: adaptamos la tecnología a tus necesidades, desde la instalación de sensores hasta el despliegue de plataformas de análisis de datos a gran escala.
- Implementación: nos encargamos de todo el proceso técnico, incluyendo la instalación de hardware, la configuración del software y la integración con tus sistemas existentes.
- Formación y soporte: aseguramos que tu equipo esté preparado para sacar el máximo partido a las nuevas herramientas digitales, con formación práctica y soporte continuo.
Conclusión
Integrar maquinaria antigua en la Industria 4.0 no solo es posible, sino que es una oportunidad clave para mantener la competitividad en un entorno industrial cada vez más conectado.
Si quieres saber más sobre cómo podemos ayudarte en este proceso, ¡no dudes en contactarnos!
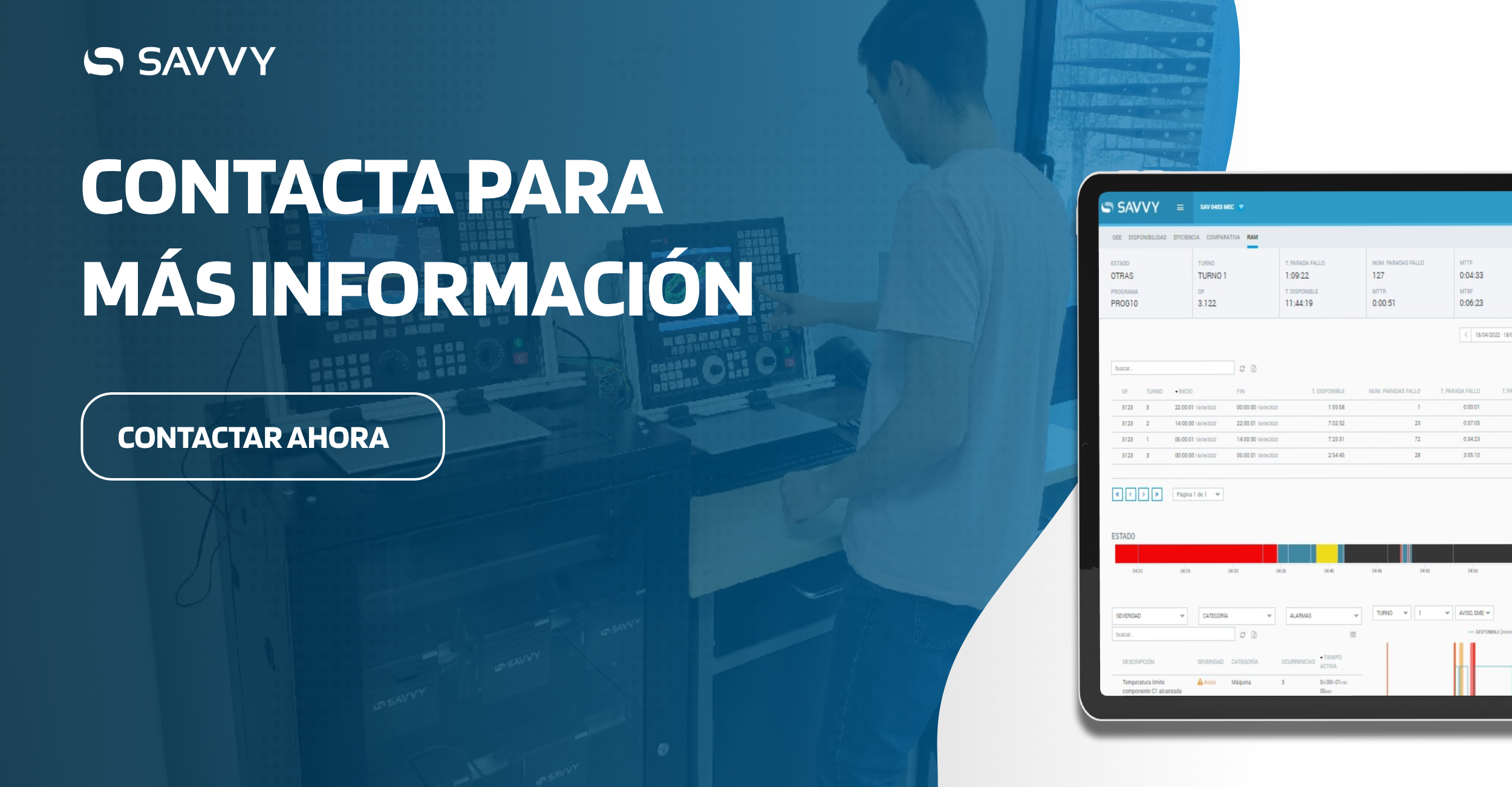
Suscríbete a nuestra newsletter
Quiero suscribirmeSUSCRÍBETE A NUESTRA NEWSLETTER